Introduction:
Diesel generators are critical assets in various industries and applications, providing reliable backup power during grid outages or serving as the primary source of electricity in remote locations. https://www.lkpowerplant.com/400kw/ and efficient operation of diesel generators is essential to ensure uninterrupted power supply and prevent costly downtime. However, like any mechanical equipment, diesel generators are prone to wear and tear over time, leading to potential failures and performance issues. To address these challenges, predictive maintenance strategies have emerged as a proactive approach to monitor and manage the health of diesel generators, optimizing their performance and extending their lifespan.
This article explores the importance of predictive maintenance for diesel generators, its benefits, key components, and best practices for implementation. By leveraging predictive maintenance techniques, organizations can improve the reliability, efficiency, and cost-effectiveness of their diesel generator assets, ultimately enhancing overall operational resilience.
Importance of Predictive Maintenance for Diesel Generators:
Predictive maintenance is a data-driven maintenance strategy that uses advanced monitoring technologies and analytics to predict equipment failures before they occur. In the context of diesel generators, predictive maintenance plays a crucial role in detecting early signs of potential issues, identifying maintenance needs, and scheduling interventions at the most opportune times. By moving away from reactive or scheduled maintenance approaches, organizations can minimize unplanned downtime, reduce maintenance costs, and optimize the performance of their diesel generators.
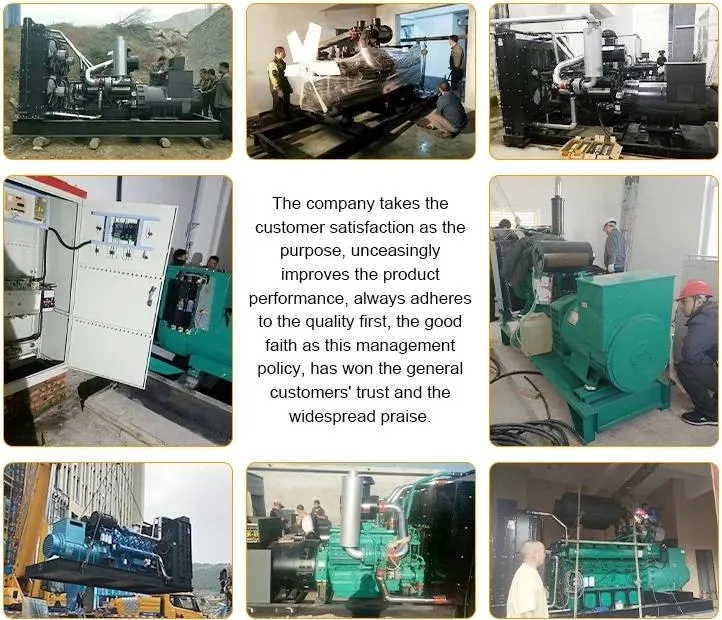
One of the primary benefits of predictive maintenance for diesel generators is the ability to detect and address problems in real-time, allowing for timely interventions and proactive maintenance actions. By continuously monitoring key performance indicators such as temperature, vibration, oil quality, and fuel consumption, maintenance teams can identify abnormal patterns or deviations from expected values, indicating potential faults or failures. This early detection enables organizations to take corrective actions before a breakdown occurs, preventing costly repairs, outages, and operational disruptions.
Furthermore, predictive maintenance helps organizations optimize their maintenance schedules and resource allocation by prioritizing maintenance tasks based on actual equipment condition and performance data. By moving away from fixed or calendar-based maintenance intervals, organizations can reduce unnecessary maintenance activities, extend the lifespan of critical components, and minimize the risk of over-maintenance or under-maintenance. This targeted approach improves the efficiency of maintenance operations and maximizes the availability and reliability of diesel generators.
Key Components of Predictive Maintenance for Diesel Generators:
Predictive maintenance for diesel generators relies on a combination of monitoring technologies, data analytics, and maintenance strategies to assess the health and performance of the equipment. The key components of a predictive maintenance program for diesel generators include:
1. Condition Monitoring Systems: Condition monitoring systems are instrumental in collecting real-time data on various parameters such as temperature, pressure, vibration, and oil quality to assess the operational condition of diesel generators. By installing sensors and monitoring devices on critical components, maintenance teams can track equipment performance, detect anomalies, and generate alerts when abnormalities are detected.
2. Data Analytics and Predictive Modeling: Data analytics tools and predictive modeling techniques are used to analyze the vast amounts of sensor data collected from diesel generators and predict potential failures or performance degradation. By applying machine learning algorithms and statistical analysis to historical data, organizations can identify patterns, trends, and correlations that indicate impending issues and develop predictive maintenance strategies.
3. Remote Monitoring and Diagnostics: Remote monitoring capabilities enable maintenance teams to access real-time equipment data from anywhere, allowing for proactive monitoring, troubleshooting, and diagnosis of diesel generator performance. By leveraging remote monitoring technologies, organizations can minimize the need for on-site inspections, streamline maintenance processes, and respond swiftly to emerging issues.
4. Condition-Based Maintenance Strategies: Condition-based maintenance (CBM) strategies focus on monitoring specific parameters or indicators that reflect the health and performance of diesel generators, triggering maintenance actions when predefined thresholds are exceeded. By adopting a CBM approach, organizations can tailor maintenance activities to the actual condition of the equipment, optimizing resource utilization and minimizing unnecessary maintenance interventions.
Best Practices for Implementing Predictive Maintenance for Diesel Generators:
Successful implementation of predictive maintenance for diesel generators requires a systematic approach that integrates technology, processes, and expertise to optimize equipment performance and reliability. To effectively establish a predictive maintenance program for diesel generators, organizations should consider the following best practices:
1. Define Clear Objectives and Key Performance Indicators (KPIs): Before implementing predictive maintenance, organizations should clearly define their objectives, goals, and key performance indicators to measure the success of the program. Whether the focus is on reducing downtime, improving reliability, or optimizing maintenance costs, establishing clear KPIs ensures alignment with business priorities and enables effective monitoring of program outcomes.
2. Select Appropriate Monitoring Technologies and Sensors: The selection of monitoring technologies and sensors plays a crucial role in the effectiveness of predictive maintenance for diesel generators. Organizations should evaluate available options based on factors such as accuracy, reliability, compatibility with existing systems, and ease of integration. Choosing the right sensors and monitoring devices ensures accurate data collection and actionable insights for maintenance decision-making.
3. Implement Data Integration and Analysis Platforms: To leverage the vast amounts of data generated by condition monitoring systems and sensors, organizations should invest in data integration and analysis platforms that enable data aggregation, visualization, and analytics. By centralizing equipment data and applying advanced analytics tools, maintenance teams can uncover hidden patterns, trends, and anomalies that indicate equipment health and performance issues.
4. Develop Predictive Maintenance Algorithms and Models: Building predictive maintenance algorithms and models tailored to the specific characteristics of diesel generators is essential for accurately predicting failures and optimizing maintenance strategies. Organizations should collaborate with data scientists, reliability engineers, and domain experts to develop predictive models that consider multiple variables, historical data, and equipment operating conditions to forecast potential failures.
5. Establish Proactive Maintenance Workflows: Proactive maintenance workflows enable maintenance teams to receive real-time alerts, notifications, and recommendations based on equipment performance data, facilitating timely interventions and preventive maintenance actions. By automating maintenance workflows and integrating predictive maintenance insights into work order management systems, organizations can streamline maintenance processes and improve response times to emerging issues.
6. Train Maintenance Teams and Ensure Continuous Improvement: Effective implementation of predictive maintenance requires adequate training for maintenance teams on new technologies, tools, and processes. Organizations should invest in training programs, workshops, and knowledge sharing sessions to equip maintenance personnel with the skills and expertise needed to interpret data, make informed decisions, and execute maintenance tasks effectively. Additionally, organizations should foster a culture of continuous improvement by encouraging feedback, learning from past experiences, and adapting maintenance strategies based on performance outcomes.
7. Monitor Program Performance and Evaluate Results: Monitoring the performance of the predictive maintenance program for diesel generators is crucial to assess its effectiveness, identify areas for improvement, and measure the impact on equipment reliability and performance. Organizations should regularly evaluate key performance indicators, track maintenance costs, measure downtime reduction, and solicit feedback from maintenance teams to gauge the success of the program and make informed decisions for future enhancements.
Conclusion:
Predictive maintenance for diesel generators offers organizations a proactive and data-driven approach to optimize equipment performance, reduce downtime, and enhance operational efficiency. By leveraging advanced monitoring technologies, data analytics tools, and predictive modeling techniques, organizations can detect early signs of potential failures, prioritize maintenance activities, and extend the lifespan of critical components. Implementing a comprehensive predictive maintenance program for diesel generators requires a strategic alignment of objectives, selection of appropriate monitoring technologies, development of predictive maintenance algorithms, and continuous training and improvement initiatives.
As organizations strive to improve the reliability, availability, and cost-effectiveness of their diesel generator assets, predictive maintenance emerges as a valuable tool to maximize operational resilience and mitigate risks associated with equipment failures. By embracing predictive maintenance best practices and fostering a culture of innovation and continuous improvement, organizations can unlock the full potential of their diesel generators and ensure uninterrupted power supply in a dynamic and demanding operational environment.